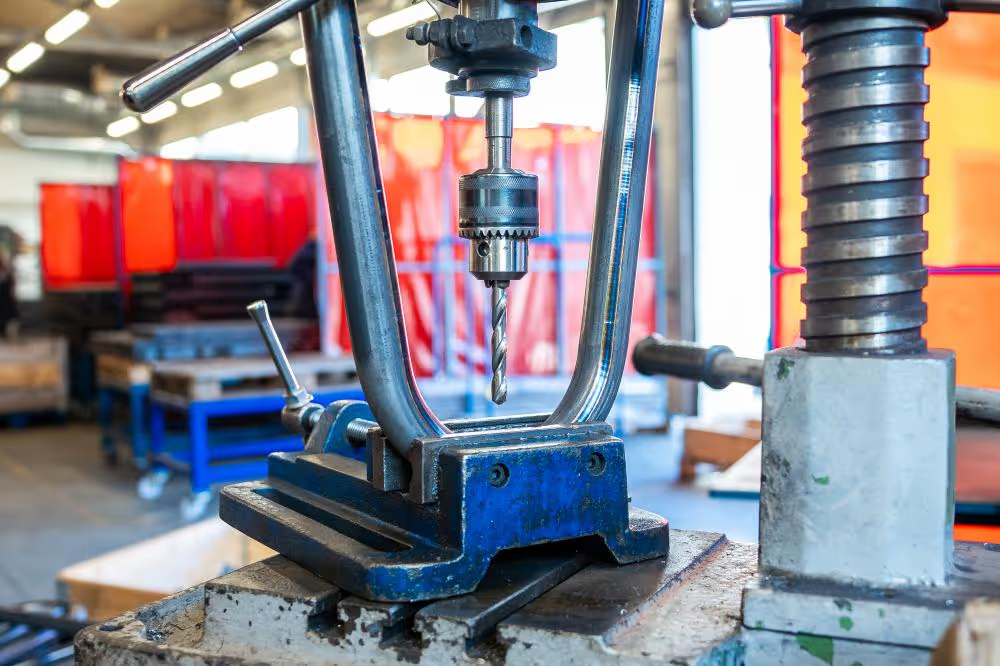
The Importance and Basics of Tapping with a Drill Press
Tapping with a drill press is a crucial process in metalworking, allowing machinists to create threads within pre-drilled holes. This process is indispensable when constructing parts that require precise threading for bolts or screws. Understanding the dynamics of tapping can significantly impact the efficiency and quality of threaded components.
The correct use of drill presses for tapping enhances productivity, especially in industrial applications. By implementing this technique, manufacturers can achieve higher precision and consistent results, which is particularly important for mass production. Incorporating automated systems further boosts efficiency and reduces the margin for error.
Choosing the Right Equipment for Tapping with a Drill Press
When selecting equipment for tapping with a drill press, it is essential to consider the material being worked with and the specific requirements of the task. AutoDrill offers a range of products, including multiple spindle heads and self-feeding drills, designed to cater to diverse needs.
Ensuring that the chosen drill press and accessories are compatible with the workpiece material is vital. Various metals and materials require different speeds and forces, and selecting the wrong equipment can lead to poor quality threads or damage to the machinery.
Types of Drill Presses for Tapping
Various types of drill presses can be utilized for tapping, each with unique features and applications. Radial drilling machines, for instance, offer extensive flexibility in terms of reach and operation, making them ideal for large or awkward workpieces. Gang drills, on the other hand, provide multiple drilling options simultaneously, enhancing efficiency.
AutoDrill's range of tapping equipment includes production tapping machines designed for high-speed operations. These machines are ideal for environments requiring rapid, repetitive tapping tasks, ensuring speed without sacrificing accuracy. For less frequent operations or smaller workshops, a standard drill press with a tapping attachment may suffice.
Step-by-Step Process: Tapping with a Drill Press Atlanta GA
To begin tapping, the operator must first select the appropriate tap size for the hole and the material. The drill speed should be adjusted based on the material—faster for softer metals like aluminum and slower for harder metals like steel. Applying a tapping lubricant will reduce friction and extend tap life.
With the drill press set to the correct RPM, the operator should align the tap with the pre-drilled hole carefully. The spindle must rotate in a forward direction, lightly pressing the tap into the hole. As the tap cuts threads, reversing the spindle occasionally helps break chips and prevent binding.
Always ensure the tap is withdrawn carefully after reaching the desired depth. Maintaining constant pressure during withdrawal prevents thread damage. Checking the threads with a gauge or bolt can confirm the precision and integrity of the tapping operation.
Troubleshooting Common Tapping Issues
One frequent issue during tapping with a drill press is tap breakage, often caused by excessive speed or incorrect material handling. Reducing the drill speed and using proper lubrication can mitigate this problem. Additionally, ensuring the workpiece is securely clamped can prevent movement during operation.
Another common concern is thread tearing, which can occur if the tap is forced or withdrawn too abruptly. To avoid this, operators should use a gradual tapping approach and employ chip breaks by reversing the spindle periodically.
If threads are too loose or too tight, it may be due to improper tap selection or wear. Regular inspection and maintenance of taps are essential to ensure consistent, high-quality results.
Safety Tips for Drill Press Tapping
Safety is paramount when operating a drill press for tapping. Operators should always wear proper personal protective equipment, including safety glasses and gloves, to protect against metal shavings and potential tap breakage.
Maintaining a clean workspace is also vital. Metal shavings and debris should be cleared regularly to prevent accidents. Additionally, ensuring all equipment is correctly maintained and free of defects reduces the risk of malfunctions during tapping.
Advanced Tapping Techniques
Advanced machinists may explore techniques such as peck tapping, which involves short, controlled bursts of tapping to manage chip evacuation more effectively. This method is particularly useful for deep or blind holes, where chip accumulation could otherwise cause tap breakage.
Automated tapping systems offered by AutoDrill provide consistent, high-speed threading capabilities. These systems are designed for environments where throughput and efficiency are paramount, enabling manufacturers to handle large volumes with ease.
The Role of Automation in Tapping with a Drill Press
Automation plays a critical role in modern tapping processes, dramatically increasing throughput while minimizing human error. Systems with programmable tapping cycles allow for precise control over speed, depth, and torque, ensuring optimal performance for each specific task.
AutoDrill's advanced automation solutions integrate seamlessly with existing manufacturing setups. These systems are designed to enhance productivity, providing a competitive edge in today's fast-paced industrial landscape. By automating repetitive tasks, companies can focus more on quality assurance and innovation.
Anecdotal Insights and Experiences from Industry Professionals
Machine operators often describe a steep learning curve when mastering tapping with a drill press. An experienced technician in Atlanta once shared how software updates on their AutoDrill system revolutionized their tapping operations, reducing setup time by 50%.
Another workshop supervisor recounted the challenges of introducing automation, noting that despite initial resistance, the increased efficiency and reduced workload quickly won over the team. Industry professionals agree that the investment in quality equipment like AutoDrill's pays off in long-term savings and improved output.
Ultimately, the ability to adapt to new technologies and techniques remains a key driver of success in tapping with a drill press. As more companies in Atlanta and beyond embrace automation, the future of precision metalworking looks increasingly promising.
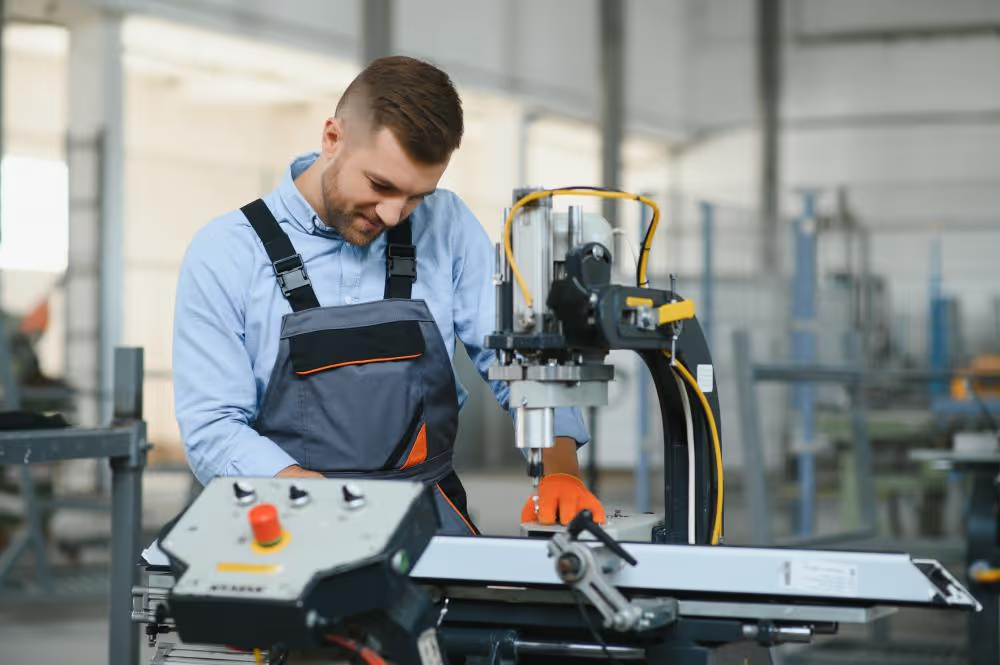
Can I use a drill press to tap?
Absolutely, you can use a drill press for tapping, and it's actually a common and effective method, especially in industrial settings. A drill press provides a stable platform and controlled movement, which are essential for precision when creating threads in metal or other materials. Think of it like using a sewing machine instead of hand-stitching; the consistency and speed you gain are significant. However, it's crucial to ensure that your drill press is compatible with the tapping task, considering factors like the size and material of the tap. AutoDrill offers various solutions tailored for these specific needs, with equipment like self-feeding drills and multiple spindle heads, which enhance both precision and efficiency. Have you ever tried using a drill press for tapping, or is this your first exploration into automated solutions?
What speed should a drill press be for tapping?
The speed of a drill press during tapping is paramount and varies based on the material you are working with. For softer metals like aluminum, higher speeds can be used, whereas harder metals like steel require slower speeds to prevent tap breakage. A general rule of thumb is to prioritize control over speed to ensure quality threads. AutoDrill equipment, known for its precision, offers adjustable speed settings to accommodate various tapping operations. Imagine you're driving on a highway; different conditions require different speeds for safety and efficiency—tapping works in a similar way. Would you like to know more about how speed adjustments can optimize your operations?
Can tapping be done on a drilling machine?
Yes, tapping can indeed be done on a drilling machine, but there are nuances to consider. Many modern drilling machines, like those from AutoDrill, are equipped with features specifically designed for tapping, such as reversing capabilities and adjustable torque settings. Using a standard drilling machine without these features might lead to inefficiencies or errors in the tapping process. It's akin to using a computer for graphic design—you need the right software and tools to achieve the best results. If you're using your current equipment, consider whether an upgrade might enhance your tap operations and overall productivity. What's your current setup like, and have you noticed any limitations?
How to tap threads with a drill?
Tapping threads with a drill involves a series of precise steps. First, ensure you have the correct tap size for the pre-drilled hole and the material you are working with. Next, set the drill press to the appropriate speed—faster for softer materials, slower for harder ones. Apply a tapping lubricant to reduce friction and extend the life of your tap. Carefully align the tap with the hole, engage the spindle in the forward direction, and press the tap gently into the hole. Occasionally reverse the spindle to break chips and prevent binding. Once the desired depth is achieved, withdraw the tap with consistent pressure to avoid damaging the threads. This process is similar to assembling a jigsaw puzzle—each piece must fit perfectly, or the final result won't be accurate. Have you ever experienced challenges while tapping, and how did you overcome them?
What are common tapping issues and how can they be resolved?
Some common tapping issues include tap breakage, thread tearing, and inconsistent thread sizes. Tap breakage often results from excessive speed or improper handling of materials. This can be mitigated by reducing speed and using appropriate lubrication. Thread tearing generally occurs when the tap is forced or withdrawn abruptly; a gradual approach with frequent spindle reversal can help manage this. Inconsistencies in thread size might indicate a need for better tap selection or maintenance checks to ensure tap integrity. Consider these issues as akin to problems you might face when maintaining a car; regular attention and correct handling prevent long-term damage. What troubleshooting methods have you found effective in your own experience?
How does automation impact tapping efficiency?
Automation dramatically enhances tapping efficiency by minimizing human error and increasing throughput. With programmable cycles, automation allows precise control over variables like speed, depth, and torque, optimizing each tapping operation. AutoDrill's automation systems, for example, integrate seamlessly with existing setups and enable manufacturers to handle large volumes efficiently. Imagine a bakery that adopts automated mixers—they can produce consistent results faster than with manual labor. In tapping, automation similarly streamlines processes, allowing for more focus on quality assurance. How might integrating automation improve your current production capabilities?
Resources
- Occupational Safety and Health Administration (OSHA) - OSHA provides comprehensive safety guidelines for drill press operation to ensure workplace safety.
- Machining Cloud - Machining Cloud offers a wealth of information on selecting the right tools and equipment for metalworking processes.
- MetalWorkingFun - MetalWorkingFun is a community forum where industry professionals share insights and experiences related to metalworking processes.
- National Institute of Standards and Technology (NIST) - NIST provides standards and guidelines for industrial processes to ensure quality and precision in manufacturing.
- Associated Wire Rope Fabricators (AWRF) - AWRF offers valuable resources on industrial equipment and tools, including drill presses and tapping equipment.