5k Series
Designed for automatic drilling of larger holes and other heavy duty operations.
Overview
The 5k Series AutoDrill is designed for automatic drilling of larger holes and other heavy duty operations. It comes standard with features that make it easy to setup, adjust and maintain. All operations are performed with a standard electric motor and a small volume of shop air. This keeps the operating costs to a minimum.
Uses and Features
- Plate and structural steel hole drilling
- Drilling multiple holes with a single unit
- Flow drilling or form drilling of holes
- High thrust applications
- Multi-wall drilling operations that require SkipFeed
- Deep hole operations up to 6.000″
- Precision depth control drilling applications
- Operations requiring all position mounting
- Operations requiring through the spindle coolant
- Morse Taper tooling requirements
- Available with air motor drives for explosion-proof operations using inert gas
5k Series Units
Build your drill your way
5k Series Motor Configurations
We recommend a three phase electric motor for its’ simple, reliable, and energy efficient operation. If you do not have three phase power available, a single phase motor option is also available. You can also choose an air motor drive for the unit if you are in an all air shop or have a space constraint, etc.
This page will show some basic motor configurations. It will use the electric motor as an example, but the pneumatic motor drive options are similar. Motors for the 5000 Series AutoDrill are generally available from 1/3 HP to 3 HP. Almost all motor drive arrangements can also make use of a gear reducer for lower RPM applications.
Almost all 5000 Series self feeder AutoDrill units are driven by high quality, anti-slip HTD timing belt and pulley set-ups. These are toothed sets for positive drive action.
Typical Motor & Automatic Drill Drive Arrangements:
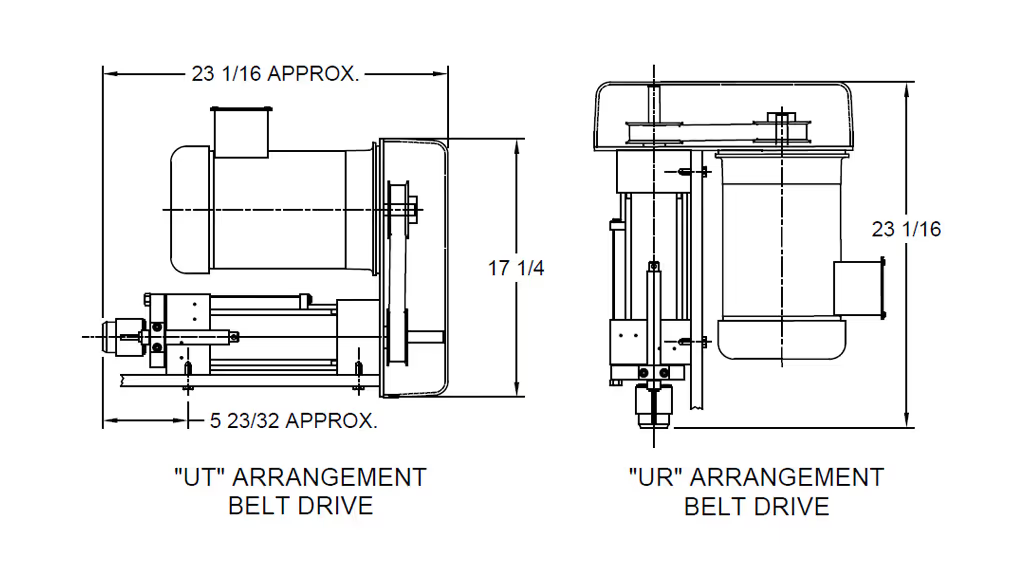
This shows the “UT” and “UR” motor configuration. These are the most common. “UT” is often for horizontal drilling and “UR” generally for vertical. The motor is generally configurable in four positions with this mounting plate. Custom positions also available upon request.
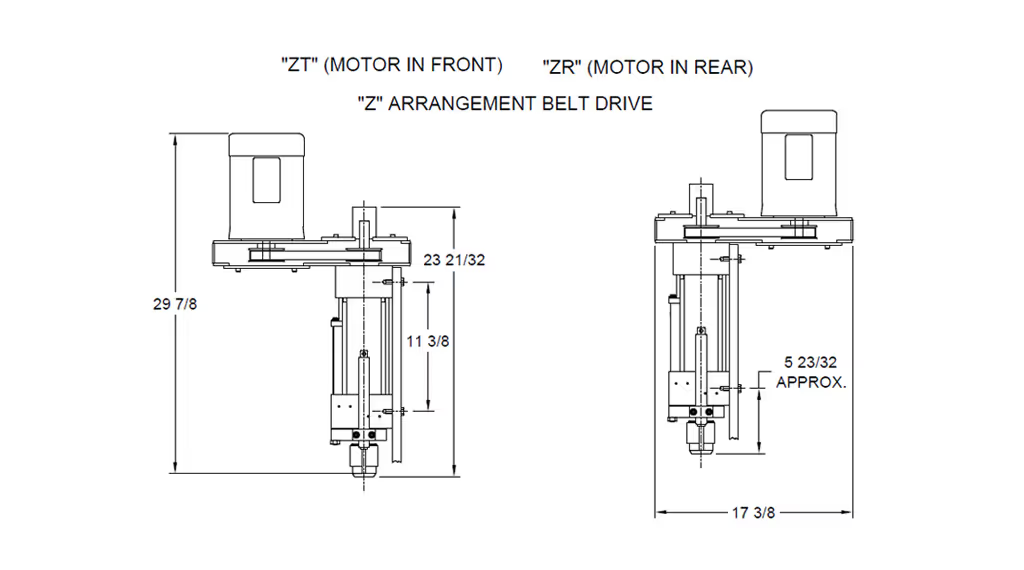
This shows the “ZT” and “ZR” configuration. “ZT” is common for horizontal drilling operations. “ZR” is common for vertical operations. Both can be set up to put the motor out of the way of other processes. Custom rotation positions available upon request.
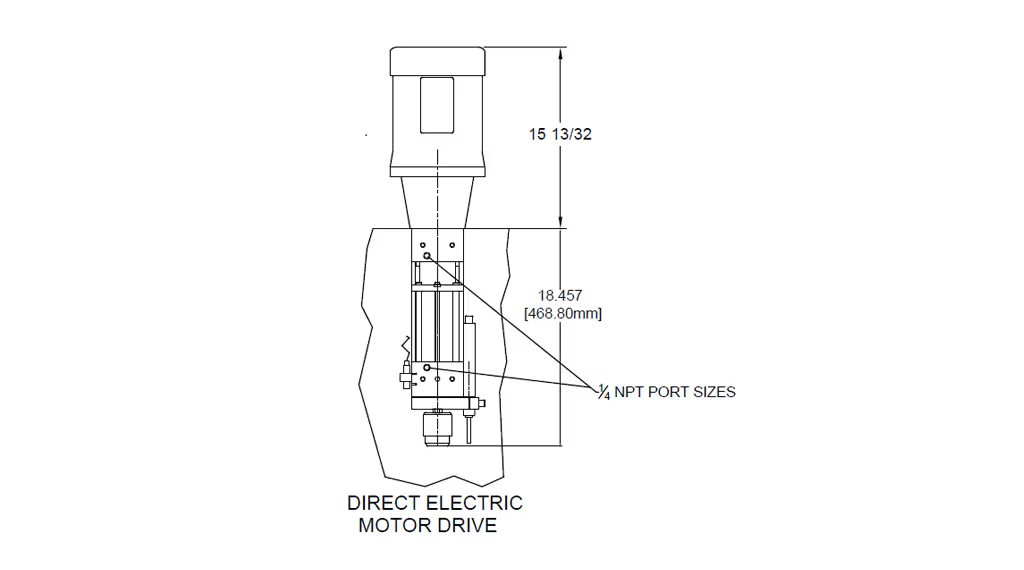
Direct Drive configuration. The output speed of the motor is often the same as the tool RPM with this configuration.
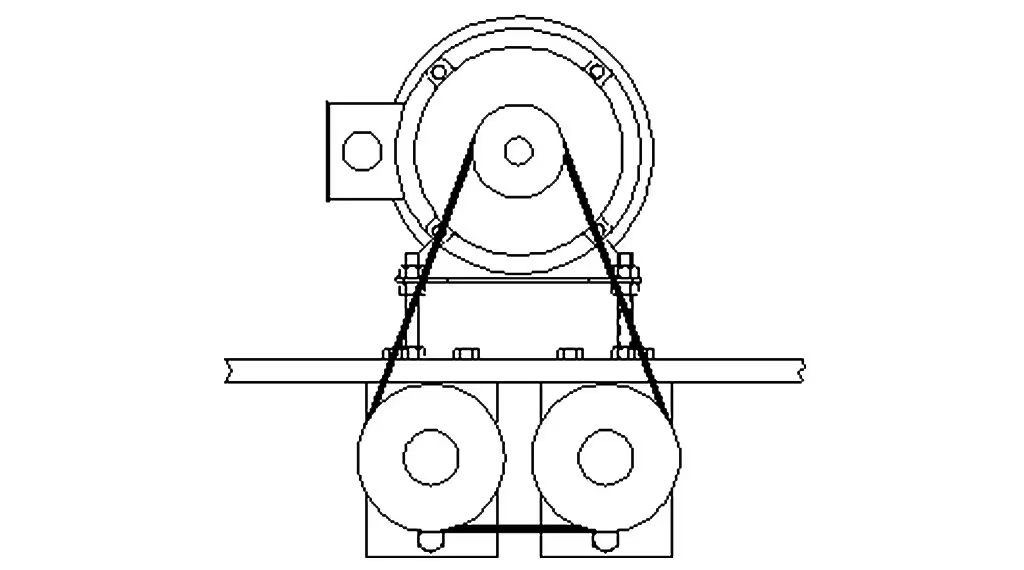
Custom Multiple Drive Arrangement. If you have a special need, please contact us. We can often meet that need. Some other offerings include off-set drives, close C-C drives, right angle drives, etc.
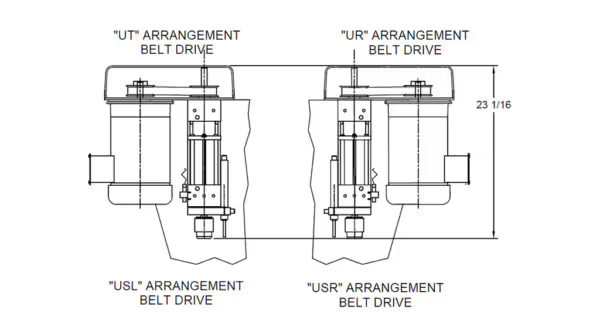
This shows the “USL” and “USR” configuration. This puts the drill motor off to the side for clearance and convenience purposes.
Electric Motor Advantages:
- Industry standard
- Many different suppliers available
- Inexpensive to purchase
- Saves you the most money in many cases
- Very reliable
- Simple to maintain
- Constant and predictable RPM at the tool
- VFD / Inverter rated options available for different RPM rates
- Low noise operation
- A very “green” option
Air Motor Advantages:
- Weighs less
- Small size
- Can possibly alter RPM rate easily while in use
- No electrical power is needed except at compressor
- Compatible with wood and plastic “pneumatic only” shops
- Inert gasses can be utilized for explosion-proof or other critical operations
5k Series Annular Cutting Machine
The 5000 Annular Cutter Machine by AutoDrill is offered for large hole operations, structural steel drill processes, plate drilling, pipe drilling, multiple hole drilling, etc. It is based off of our 5000 series unit which is the most robust self stroking drill unit we offer. The features on the 5000 annular cutter machine make it simple to operate and maintain. Adjusting the unit for different size holes or thicknesses of material is simple and fast. By choosing a three phase electric motor drive, the operating costs are kept to a minimum. Single phase and air motor options also exist.
If you want to save money and time by becoming more efficient or you want to simply make more product with less resources, this machine is our answer for maximum cost savings and higher production capabilities.
Some of the many uses for the 5000 Annular Cutter Machine are:
- Structural Steel drilling (I-beams, channel, etc.)
- Plate drilling
- Pipe drilling (including well pipe)
- Higher thrust applications (up to 1500 lbs. on standard shop air)
- Large hole drilling operations
- Depth controlled drilling applications
- Operations requiring all position mounting
- Operations requiring through the spindle coolant
- Preparation for machining large holes by removing a majority of the material beforehand
- Heat exchanger and heat plate manufacturing
- Accurately drill large tap drill size holes +0.005 / -0.000″
- Available with air motor drives for explosion-proof operations using inert gas
Some of the 5000 Annular Cutter Machine’s main features are:
- Self feeder drill abilities
- Less time and energy are consumed as compared to standard twist drill hole processes
- Annular cutter drills are “green” in comparison to standard tooling
- Faster feed rates are achieved with more cutting teeth and less tool wear
- Lighter and less powerful drilling equipment can be used with annular cutters as opposed to typical drilling operations of the same size and diameter
- More accurate than conventional twist drill operations on hole size, location, etc.
- Coolant through the center of the tool leads to better lubrication, longer tool life and a cleaner process
- Spring loaded plug ejection options (no more stopping the machine to dig out the slug from a hole saw type tool!)
- Can receive and drive multi-head devices in some cases
- Accurate tool speeds and feeds
- Drill unit stroke from minimum to 6.000″ (152mm)
- Up to 6.000″ (152mm) of HydroSpeed feed control
- Custom configurations for close center to center drilling
- Built in depth control that is both adjustable and accurate
- Can be mounted to operate in any direction
- Electric or Pneumatic (air) motor drives up to 5 HP standard
- Remove annular cutting tools to make use of standard key-type chucks if desired
Annular cutters are preferred over twist drills for large hole processes because they cut a cleaner, more efficient hole. The cutter cuts only the outside diameter of the hole creating less stress on the drill machine. The multiple cutting edges or surfaces allow for increased feed rates and typically a cleaner hole.
5k Series AutoTap
The 5000 Series Self-Feeder Auto-Tap gives you the robust AutoDrill 5160 unit as a driver for a Self-Reversing tapping head. This may allow a single unit to be used for both tapping and drilling at times. Because the Self-Reversing tap head is being used, there is no need for the motor drive to change rotation. The Auto-Tap is capable of any thread configuration within its capacity range and almost always without a single change to the equipment other than adjustments to the feed control, etc.
Many of the ball screw and lead screw units on the market require that you change out physical parts (expensive and time consuming!) to change from one tap size to another. This is a tremendous advantage to a job shop or manufacturer looking to simplify their process and keep inventory under control. These automatic tapping machines can be configured for different size tap operations or different thread pitches very quickly. Cost is kept to a minimum while reliability and efficiency is increased.
Here are just some of the features and options for the Control-Feed Auto-Tap:
- Only AutoDrill offers the Control Feed advantage!
- Positive forward and reverse drive
- Compatible with multiple spindle tap operations for complex or closely spaced patterns, etc.
- Entry cushion for reliable work contact
- Entry cushion also helps minimize cross threading on re-threading or thread chasing operations
- Compatible with roll tap, thread forming or cut tap operations
- Four models handle up to 1-1/8″ (Metric: M28) capacity (cut tap)
- Most often equipped with a Rubber-Flex collet
- Optional quick change spindle option
- Dual direction hydraulic feed control for precise process control during entry, exit, and free travel.
- Optional SkipFeed for DrillTap (DRAP) or fast cycle time applications
- Factory assembled and tested
Auto-Tap Standard Selection
- Auto-Tap Rx30 (up to 1/4″)
- Auto-Tap Rx II 50 (up to 1/2″)
- Auto-Tap Rx70 (up to 5/8″)
- Auto-Tap 90X (up to 1-1/8″)