Tapping Different Thread Pitches On The Same Machine
Using a Multi-Drill Tapping Head to work on a pattern that has more than one thread pitch is sometimes necessary. The example photo is a five hole pattern in a bolt Circle (BCD or PCD) layout. Imagine that two holes need to be tapped 1/4-28 and the other three holes will be tapped 3/8-24. On a standard multiple spindle tapping head, the output spindles all rotate at the same speed. Because the 1/4-28 tap will feed slower than the 3/8-24 tap while in the material, this simply will not work. This will cause tap breakage with rigid tap collets.
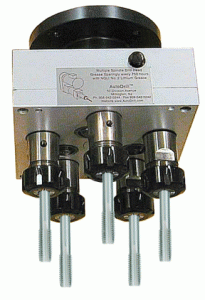
AutoDrill has a number of solutions we apply for such circumstances.
At times, the internal gearing can be adjusted to set the RPM of the 1/4-28 tap spindles to turn at 7/6 the rpm of the 3/8-24 spindles. This will allow the spindles for the 28-pitch tap to turn seven revolutions for every six revolutions of the 24-pitch tap’s spindles. The feed will then be equal. The holes are tapped with the multi-spindle tapping head without tap breakage. When possible, this is often the best option. However, it is not the best answer if you often change from one thread pitch to another.
For some differences in pitch custom gearing may not be possible. An example is when a metric pitch of 1.25, which in our common inch system has a feed of 0.0492″ per revolution has to be mated with a 20 pitch tap. The difference in pitch is impossible to solve by internal gearing at an affordable cost. For this type of problem, AutoDrill suggests floating tap collets or chucks that have linear float built right into the collet set-up. They are spring loaded so that when the process is complete, the tooling snaps back into the proper position for the next hole process. This solution may work for shallow depth tapping applications only and needs to be carefully considered.
If you can tap the part from opposite sides, it is possible to have a machine on top of the part tapping one thread pitch and a separate machine below the part tapping the other thread pitch. This is especially useful in high volume tapping where the time saved will pay for the additional machine.
Finally, when your multiple spindle tap head process will be used for all the same thread pitch now but will be used with a different thread pitch later, we have a solution. AutoDrill offers a Control Feed Tapper which allows for fast and simple changes from one thread pitch to another without disassembling the machine. Many lead screw tap machines require the end user to remove the “lead screw” to change to another thread pitch. AutoDrill makes it possible without such time wasting steps. Of course, there are servo-driven tapping machines on the market too, but they are many times as expensive and much harder to maintain. AutoDrill’s tapping option is often the best if you are not running an ultra-high end process, you can avoid those additional high costs by choosing the AutoDrill product. Another tremendous advantage we offer is that parts are stocked right here in the USA. Our lead times are the best in the industry for new machines or repair parts.